
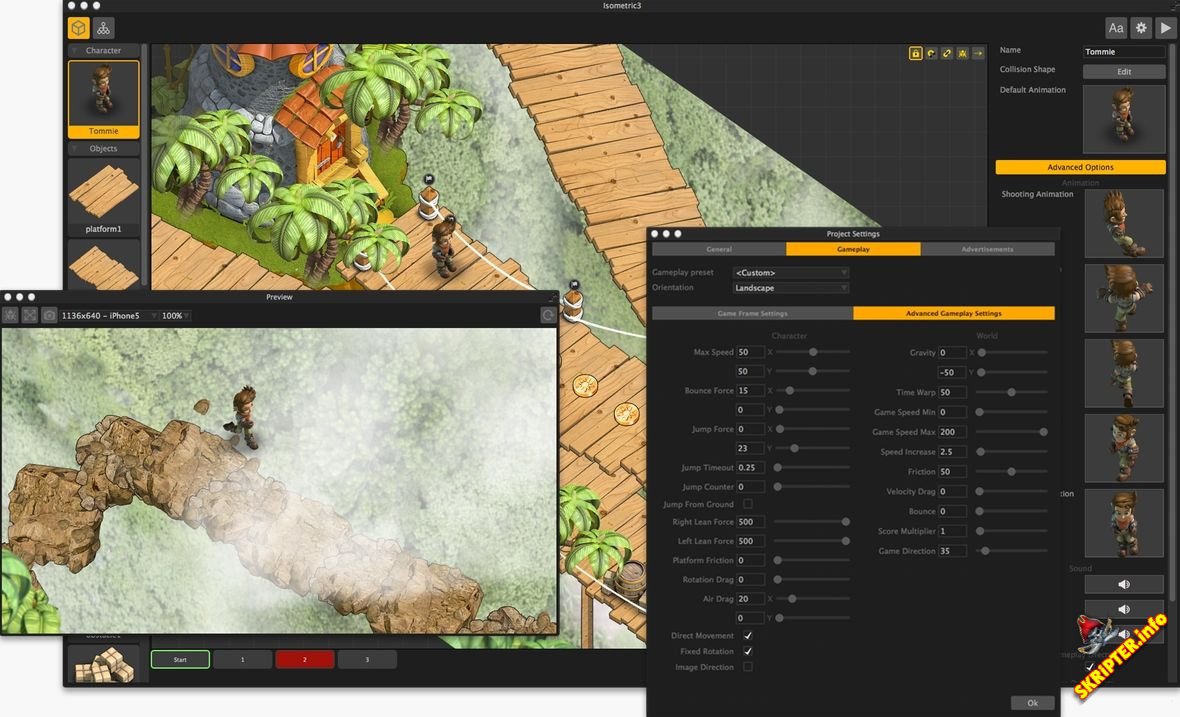
This portion of the process is best completed during the prototyping phase. For example, the device will need to pass FCC/CISPR EMC compliance testing at minimum, and another consumer or commercial standard (UL, IEC, etc.) might apply to your product. To ensure you can quickly take your box build and take the product to market, the build will still have to go through the same qualifications as any other electronic device sold on the open market. The idea is for the customer to be able to use the assembly as soon as it’s received. Functional testing, typically involving a customer-supplied fixture and automated test program.Installation of any switches, buttons, screens, or other HMI elements.Flashing of firmware/software into the main PCBA memory if components are not supplied pre-flashed.Machining any holes or openings into the enclosure for cables and harnesses.Machining a simple enclosure, usually from sheet metal, or adapting an off-the-shelf plastic/metal enclosure.Installation of the PCBA (or multiple boards) into the enclosure.Some of the steps involved in manufacturing a box build assembly might include: The enclosure itself could be an off-the-shelf enclosure, a sheet metal enclosure, or even a 3D printed box. The PCBA, its cabling and mounting, and the box itself are all assembled into a single enclosure that functions as the product’s packaging. Some manufacturers will offer box build services, where they bring many of a system together into a single package and ship you a ready-to-use assembly. They may not have the aesthetic you would expect from some of the most popular consumer products, but they are an effective option for expedited production. Sometimes known as systems integration, box builds essentially aggregate all the important elements that would appear in a finished product into a simple assembly.

I’ve talked to many designers and product developers, and many of them have never produced a new product with their CM as a box build. This overused route to a new product is a box build assembly. There is a quick way to get your product into a usable enclosure, complete with input power and cabling, and with a form factor that fits your PCBA. The enclosure, cabling and connectors, embedded software/firmware, and of course the PCBA all have to be considered in totality. When you’re ready to manufacture a new device at production volume, there are many aspects of the product that must come together.
